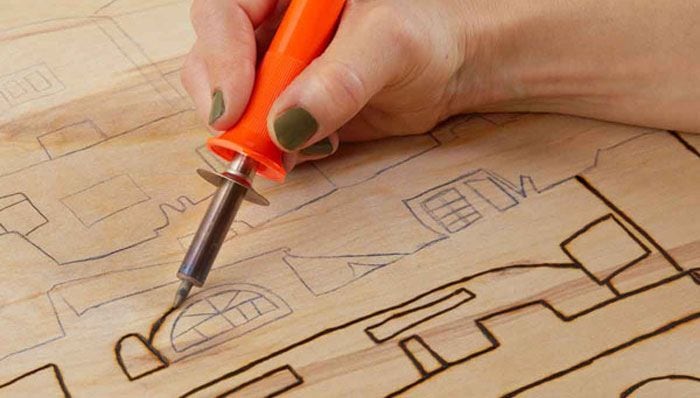
We'll be discussing Interchangeable Pyrography Nibs, Skew tips, Chisel tips, Wire nib burners and other pyrography tips. Once you've understood the basics, you can start using your pyrography pen in a creative and efficient way. Before we go on to the nibs let's take a look at what they are, and why you should be using them. We'll then discuss how to choose the right one for your project.
Interchangeable pyrography nibs
There are two types main pyrography pens: interchangeable or fixed. Fixed pens have attached tips. These are best for beginners, while interchangeable pens allow you to vary your tips to suit any project. Both styles are fast and efficient. A set of 53 bresstaps and 12 stencils can make it easier to switch to an interchangeable pen. There are many different sizes available, and the set includes both large and small nibs.
The wire-tip pens offer superior heating and burning. They also heat faster and provide more detail than standard pens. The wire-tip pen is smaller and easier than its interchangeable counterparts. Each set comes with a detailed user manual. These pens also come with a user manual. The wire-burning pyrography pens are often used by professional artists and offer an extensive set of interchangeable tips.
Skew tips
There are two main types for pyrography skewtips: rounded or ball. Ball tips can be used for carving straight lines and cursive. Ball tips take longer to heat up, cool down, but they are great for shading and general detail work. The skew tip is angled with a sharp edge at the end. Skew tip are commonly used to slice into wood. While rounded tips are often used to shade or carve uneven surfaces, they are more common.
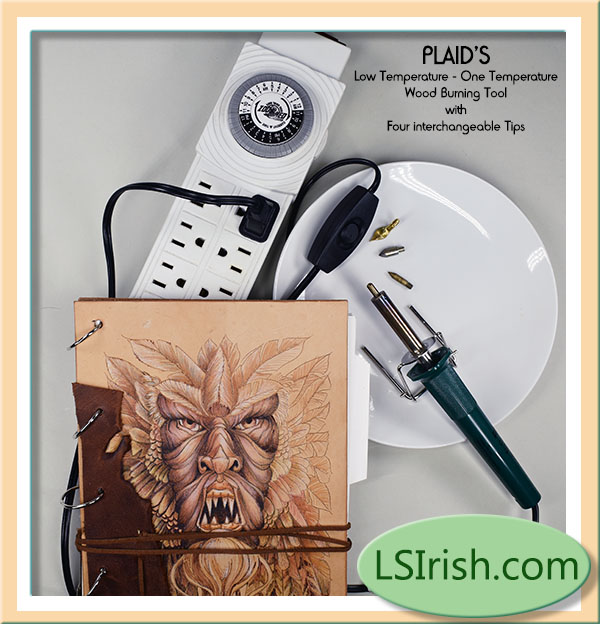
There are many options for skew tips, each with its own name and shape, but they all use high-quality Nichrome wire. For delicate lines and details, smaller tips work best. Larger tips work better for more bold designs. A variety of pen tips are used by Pyrographers. Each has a different function or texture. The best skew tip for pyrography will be found through trial and error, and experimenting with different types will allow you to choose the perfect tip for your work.
Chisel tips
A chiseltip is one of the most useful tools for pyrography. These tools are ideal for creating lines and patterns in wood or shading small areas. You can bend them to create stamped shapes. You can use different chisel tips to create burnt wood styles.
Razertip's chisel pyrography tip is a great tool for repeating lines and fine detail. They can be bent in order to fit into tight spaces. They are also available in different types of tips: writing tips, curved spear tips, and shader tips. While each tip is useful in different ways, most of them are good for writing, scribbling or drawing lines.
Wire nib burners
There are many benefits to wire nib-burners for pyrography. They're much more efficient than other pyrography tools. Because wire points can rapidly pass an electricity charge, they are a good choice for faster-paced pyrography projects. Zweiten, wire-nib instruments can be used on lighter materials like cork and gourds or thick paper. They are safer than standard-tip pens.
Wire-nib stoves can be purchased with a pen tip which allows you to remove the entire handle from the burner when the tip gets too hot. You can also purchase wire-nibs burners with temperature controls. They're generally inexpensive and available in various sizes and styles. There are a wide variety of nib styles available for these burners. So, which one is right for you? Let's look into each one more in detail.
Multi-use Pyrography Tips
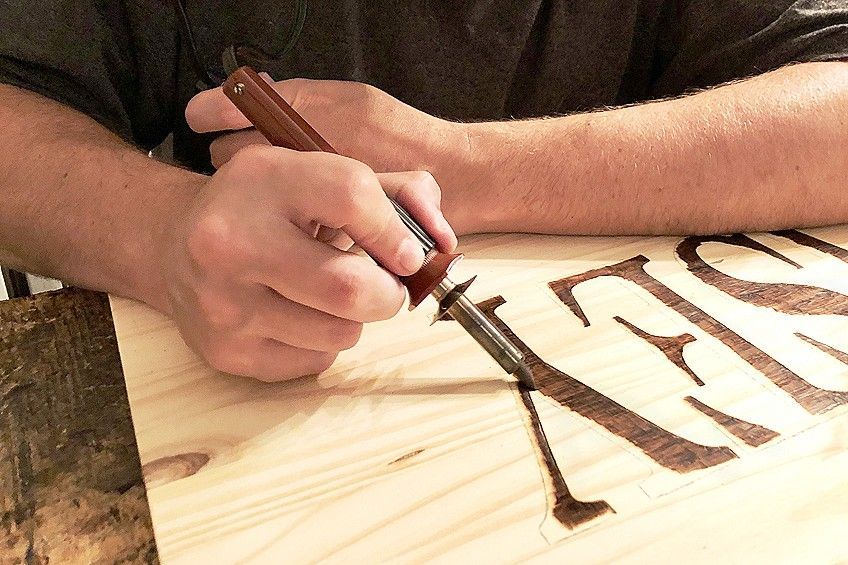
There will be a variety to choose from when you order your wood burning kits. You can choose between small, medium, large and extra-large tips depending on your desired effect. Many pyrography artists have multiple sizes and shapes to choose from for various styles and applications. It is a good idea start small with a few pen tips and build up your collection as you gain experience.
Wood burning pens include a variety tips that can be interchanged with other tools. Each tip is best for a certain job. You can also swap out the tips. These universal tips are great for beginners, and can be used for both lettering or outlining. Calligraphy tips work best for cursive text, while rounded flow tips are ideal for lettering. Other types of tips are available for wood burners who are skilled.
FAQ
What is the minimum investment a hobbyist needs to make in order to get started?
If you're looking to start your own woodworking business, you'll probably need some capital to buy the necessary tools and supplies. It's a good idea to buy a small tablesaw, drill press and circular saw. These items aren't very expensive, so you won't break the bank.
What kind of wood should I use?
The most commonly used woods for woodworking are oak, maple, cherry. Each wood type has its own characteristics which affect the final product's appearance and feel. Oak, for example, tends be darker and more hard than other woods. Birch is light and soft, while mahogany can be heavier and more dense. You can also pick between veneers and solid wood. Veneers are thin sheets of wood that are glued together to form a single layer.
How can I organize my shop?
A designated place to store your tools is the first step towards keeping your workshop clean. Keep your tools away from dust and debris, so they stay sharp and ready to work. Hang tools and accessories using pegboard hooks.
How often should I get new supplies?
You may have to replace certain tools. Hand tools will need to be sharpened regularly. If you are using power tools, you will need to purchase replacement parts regularly. Spread your purchases over several months to avoid purchasing too many items at once.
Statistics
- Woodworkers on the lower end of that spectrum, the bottom 10% to be exact, make roughly $24,000 a year, while the top 10% makes $108,000. (zippia.com)
- If your lumber isn't as dry as you would like when you purchase it (over 22% in Glen Huey's opinion…probably over 10-15% in my opinion), then it's a good idea to let it acclimate to your workshop for a couple of weeks. (woodandshop.com)
- Overall employment of woodworkers is projected to grow 8 percent from 2020 to 2030, about as fast as the average for all occupations. (bls.gov)
- Average lumber prices rose about 600 percent between April 2020 and May 2021. (familyhandyman.com)
External Links
How To
How to join wood with no nails
Woodworking is a hobby that many people enjoy doing. Woodworking is a relaxing hobby that allows you to use your hands to create useful things from wood. However, there are times when you want to join two pieces of wood together without having to use nails. This article will teach you how to do this to keep your woodwork projects looking great.
The first thing you'll need to do is cut off any rough edges from your pieces of wood before joining them together. Sharp corners can cause problems down the line. Now it's time to start glueing your boards together.
If you are working with hardwood, only one side should be glue. Use glue on both the sides for softwoods, such as cedar or pine. Press the boards down until the glue is fully incorporated. Be sure to let the glue dry before you move on to the next step.
Once you've glued your boards together you will need to drill holes in the joints to accommodate screws. You can choose the type of screw to determine the size of your holes. If you are going to use a half-inch wood screw, you will need to drill at least 3/4 inch deep.
After drilling your holes, drive the screws into the board's backside. Avoid hitting the board's top surface. Otherwise, you could ruin the finish. Don't drive the screws too far into the end. This will prevent splitting in the end grain of the wood.
You'll need to protect your completed project from the elements. To do this, you can seal the entire furniture piece or just cover the top. You want it to last years, so you can use any product. Examples include oil-based varnishes and polyurethanes, shellac, lacquer and others.
These products can usually be found at any home improvement store. Make sure you get the right product for your job. Some finishes are toxic and should not ever be used indoors. Wear protective gear whenever you are handling them.