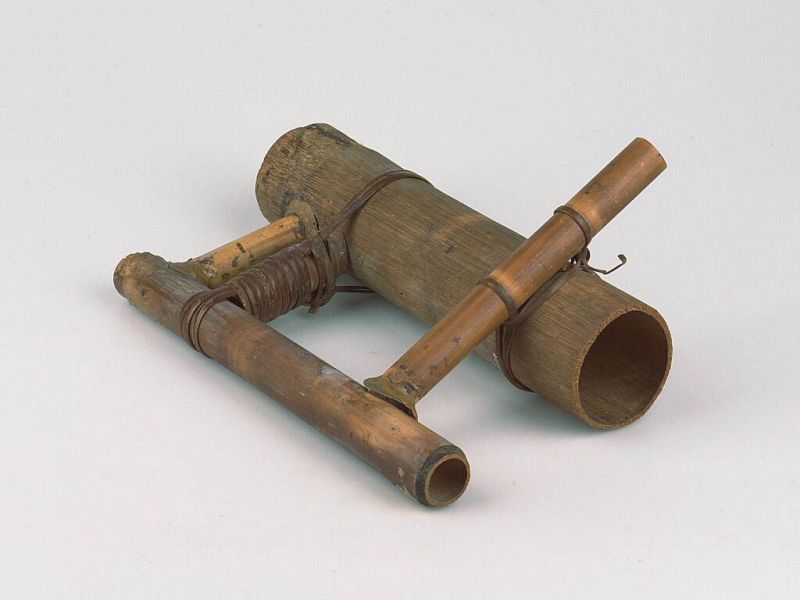
There are a few steps you should follow when installing a faceplate. These steps include choosing the right dimensions, screw size, and material. Now it is time to mount your face plate. Continue reading to find out how to install your facial plate. It will be simple to install and allow your lathe's functionality to continue as normal. The steps involved in installing a faceplate are listed below.
Dimensions
The faceplate is an accessory that can hold nearly any shape. Faceplates are not limited to wood. They can also be made from temporary materials or light alloys. These faceplates are useful for temporary use or for difficult workholding jobs. If the faceplate is made of wooden, the workpiece can attach to it using screws. This arrangement is more common for industrial lathes than home workshops.
It is crucial to know the dimensions of your faceplate. The faceplate should be exactly the same size as your blank. It is important that the screws do not conflict if you plan to use it for multiple purposes. A hole is provided for a wrench. In addition, it should have slots for a tommy bar and holes for a wrench. For each tool, it is possible to browse the faceplate.
Material
A lathe faceplate can be made from many materials, such as aluminum, cast steel, steel and welded constructions. Face plates can be made from a variety of materials. It is important that you consider their properties when choosing a material. Below are some considerations to make when selecting a faceplate material. The design process must consider specific material properties to ensure accuracy and durability. The materials used in a face plate are also important for cost optimization.
A faceplate for a lathe is typically made of a polymeric material and has a cylindrical surface. The faceplate is typically made from a polymeric material and has indicia lines, a plane front, and recesses that allow for the chucking of the workpiece. Some faceplates include fasteners in inserts of contrasting colors. This serves as an alert to the user in the unlikely event that a fastener falls out.
Screw size
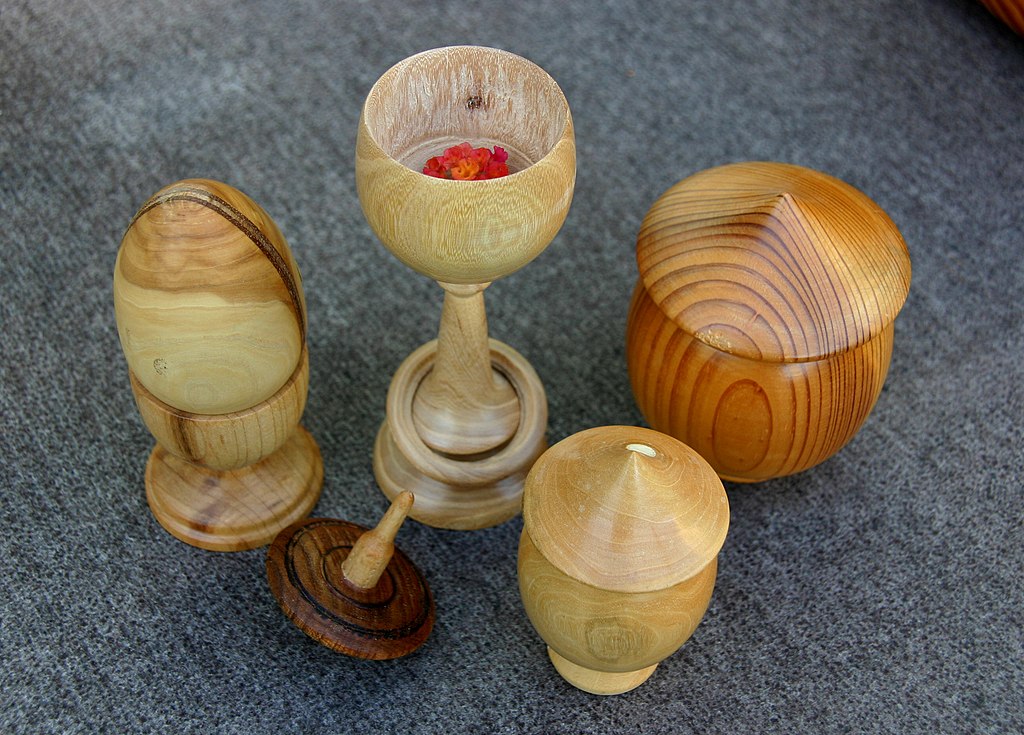
If you're using a wood lathe, you may want to consider a different screw size than you'd usually use. Because your screw size will affect the space available for your threads, If you use a bigger screw diameter, the screw will protrude from the faceplate and can cause damage. Depending on the size and shape of your lathe, you might consider a slightly concave facingplate.
Faceplates can come in a variety of sizes and materials, including alloy or steel. The smaller versions are made of alloy, while the larger ones are made of steel. The alloy faces can become worn over time, causing dangerous situations before they are discovered. Expert turners are familiar with how to mount the blanks so they do not become loose. This prevents them from being able to be turned. Beginning turners may not know how to mount their blanks properly or use too much of the tools they have.
Installation
Before you install the faceplate on your lathe make sure that the power source is turned off. Mount the faceplate onto the workpiece. Turn the spindle clockwise to turn the faceplate. Once the faceplate is in place, engage the spindle locking mechanism and turn the faceplate clockwise so that it turns freely. To remove the faceplate, disengage the spindle lock by turning the lathe counter-clockwise until it stops.
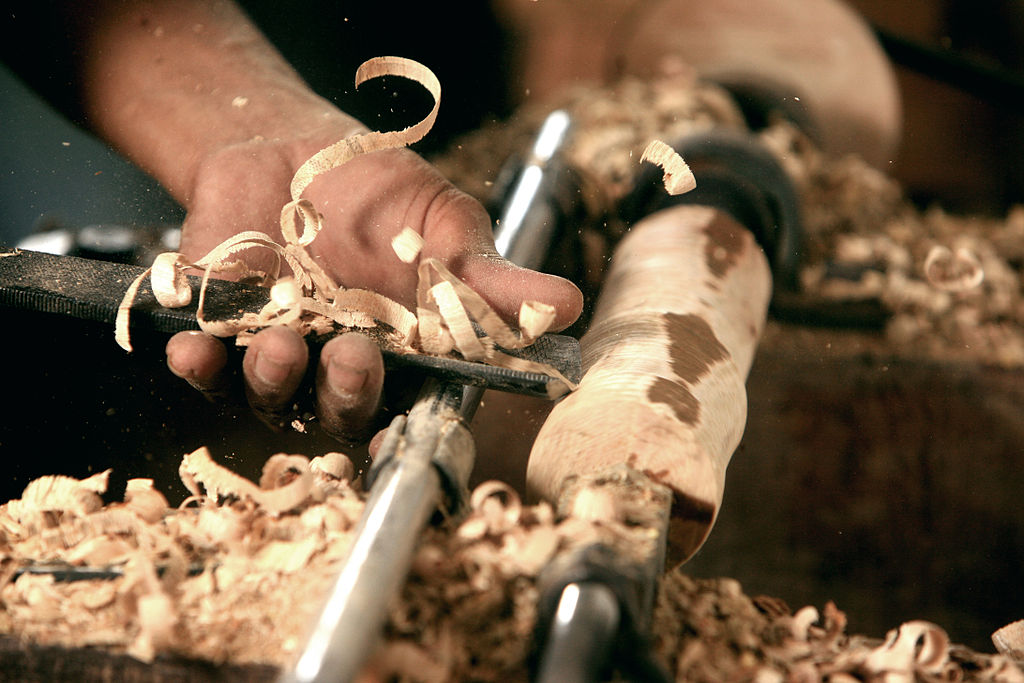
A faceplate can be described as a flat, round, and threaded plate located on the front end of a lathe. Its slotted surface accepts clamps and other fastening devices. Once the workpiece is positioned on the faceplate you can attach it by sliding the clamps through its slots or screwing them directly into faceplate's threads. After the workpiece has been placed, the faceplate is screwed on to the lathe spindle.
FAQ
Do I have the potential to make a decent living doing this?
Yes! In fact, many woodworkers already do. According to the U.S. Bureau of Labor Statistics' (BLS), in May 2012 the median annual wage of woodworkers was $34,000 That's higher than the national average of $31,000 per year.
How do I organize my shop?
To keep your workshop tidy and organized, you should first create a place for tools storage. Make sure your tools are clean and free of debris and dust so they can be used properly. Hang tools and accessories using pegboard hooks.
How can I learn basic woodworking skills
It is an excellent way to learn how to build furniture. You can make a simple bench yourself. You can do this project using any type of wood you have on hand at home. If you don't know what kind of wood to use, then go ahead and buy some cheap pine boards from Home Depot or Lowes. Once you have built your bench, you will need to sand it off and then finish it with a stain/varnish.
Statistics
- If your lumber isn't as dry as you would like when you purchase it (over 22% in Glen Huey's opinion…probably over 10-15% in my opinion), then it's a good idea to let it acclimate to your workshop for a couple of weeks. (woodandshop.com)
- The best-paid 10 percent make $76,000, while the lowest-paid 10 percent make $34,000. (zippia.com)
- Average lumber prices rose about 600 percent between April 2020 and May 2021. (familyhandyman.com)
- Woodworkers on the lower end of that spectrum, the bottom 10% to be exact, make roughly $24,000 a year, while the top 10% makes $108,000. (zippia.com)
External Links
How To
How to join wood with no nails
Many people love woodworking. Woodworking can be a fun hobby because you can work with your hands to make useful objects from wood. There are times when two pieces of wood need to be joined together. This article will show you how to do it to make your woodwork projects look great.
The first thing you'll need to do is cut off any rough edges from your pieces of wood before joining them together. Do not leave any sharp corners as they could cause problems down in the future. Now it's time to start glueing your boards together.
When working with hardwood, glue should be applied only to one side. For softwoods like cedar and pine, glue should be applied to both sides. Once you have applied the glue, press down on the boards until they are fully attached. Before you proceed to the next step, be sure to let the glue dry completely.
After you have glued your boards, drill holes where you want to insert screws. The size of these holes depends on what type of screw you choose to use. For example, if your screw is a 1/2-inch wooden screw, drill a hole that is at minimum 3/4 inches deep.
Once you have drilled the holes, the next step is to drive your screws through the joint into the board's backside. Be careful not to hit the front surface of the board, or else you'll ruin the finish. When driving the screws, try to avoid hitting the ends of the screws too much. This will avoid splitting in the wood's ends grain.
Protect your finished project now. You have two options: seal the whole furniture piece or just the top. You will want to choose a product that will be durable for many years. You can choose from oil-based varnishes or polyurethane, shellac and lacquer as examples.
These products can generally be found in any home improvement shop. You should make sure you are getting the right type for the job. Also, remember that some finishes are toxic and should never be used indoors. When handling certain finishes, wear protective gear.