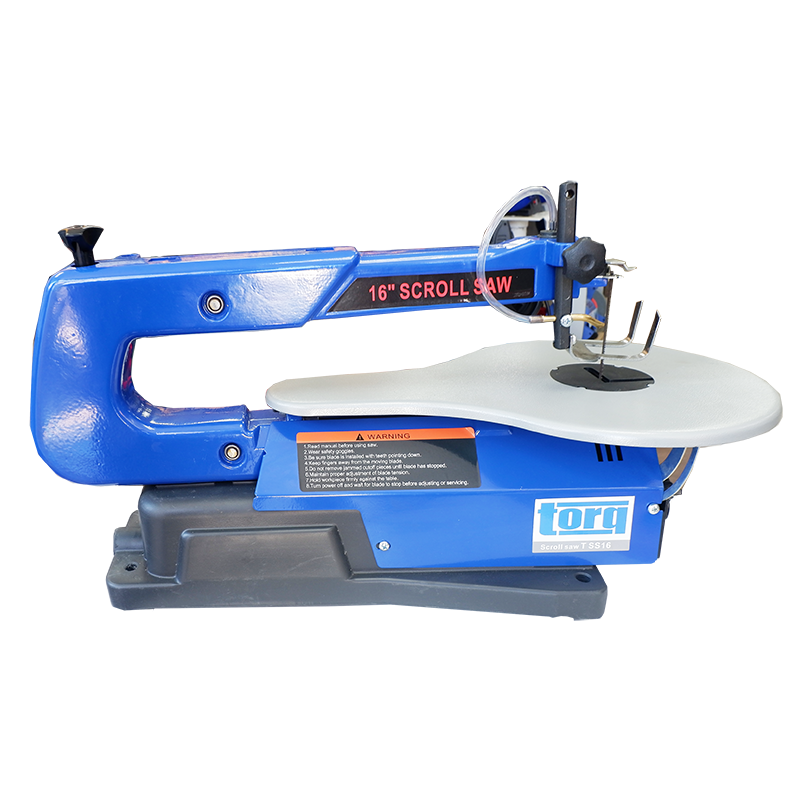
It is important that you properly tension your band saw blade before you begin to set it up. There are many methods involved and how they are set up will impact the end result of your cut. Follow these steps to setup a band saw and you will soon be cutting! Below are some tips to help maximize your bandsaw's potential. These tips may seem difficult at first but will pay off in the end.
Using a tension meter to set up a bandsaw
To ensure the best blade tension, use a tension meter. You should carefully read the instructions before you begin cutting wood. Some instructions might differ depending on the model of your saw. First, you should turn the tensionwheel down a quarter to half turn. After you have achieved this, adjust the blade guides to the recommended FSR.
Deflecting the blade is another way to test your bandsaw's blade tension. Then, listen for a distinct tone. A tension meter is a costly and precise tool that allows you to adjust the blade tension to achieve maximum blade life. A tension meter will cost around $400 but is well worth it. You don't have to buy a tension meter if you don't want one. A gauge can be used to check the tension of your blades.
A gauge is used to test the tension of the blades
A gauge is essential when setting up a bandsaw. Each blade requires the same amount tension to cut properly. The pulling force, usually between 200 and 800-pounds, will influence the amount of tension. If you don’t have one, the tension scale on a bandsaw will not give you an accurate reading. What are your options?
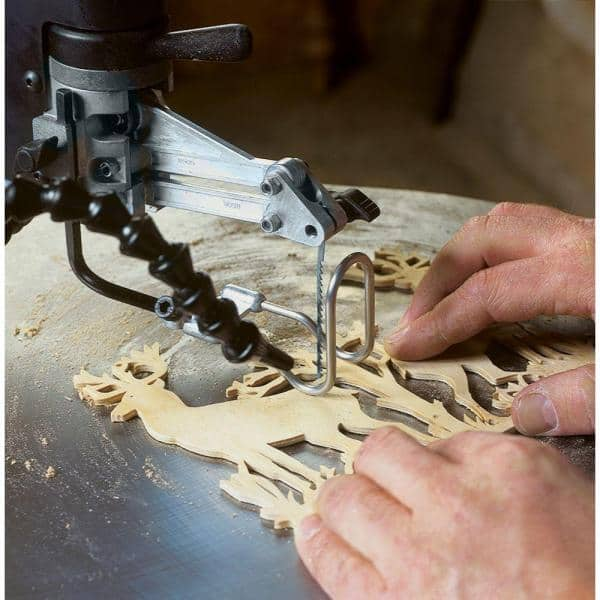
A bandsaw gauge is composed two stainless steel plates which pivot past each others and are connected using a tensioning Spring. One plate has a numeric gauge, the other a pointer indicator. Three pins attach the gauge to the blade. The gauge is attached to the blade with two pins on each side. The third pin presses against one end of the blade.
Tracking a blade
High quality cuts require proper blade setup. A successful cut requires proper blade tracking and height. Adjust the blade height so that there is approximately one-eighth - quarter-inch clearance between the material and the blade. Too low or too high a blade height can result in excessive vibration, friction, and a deviation of the line. You can use a tracking knob to control wobbling blades.
First, locate the blade. The blade should sit on the wheel's crown. In the center of the gullet, its deepest portion is. Next, tension the blade. The tracking control is usually located at back of the saw. You should apply tension to the blade. After the blade has been placed correctly, lock the control. Once you have the blade in place, you can cut.
Using a long blade to reduce drift
The long blade of a bandsaw should be placed near the crown. It should also not be too close or too far from the wheel's front or back edges. A normal blade should be positioned about an eighth to quarter inch off the center. But if your blade touches the wheel barely, it could pose a problem. Adjust the fence and tilt your upper wheel to fix this.
It is important to have the same toe-out angle for the band saw blade as you are cutting to reduce drift. This will decrease drift which is when material is lost as a wood cutter begins cutting the first piece of lumber. In the video below, you'll learn one way to set the fence angle properly. A jig is also an option to duplicate the fence angles.
Align the blade using a fence
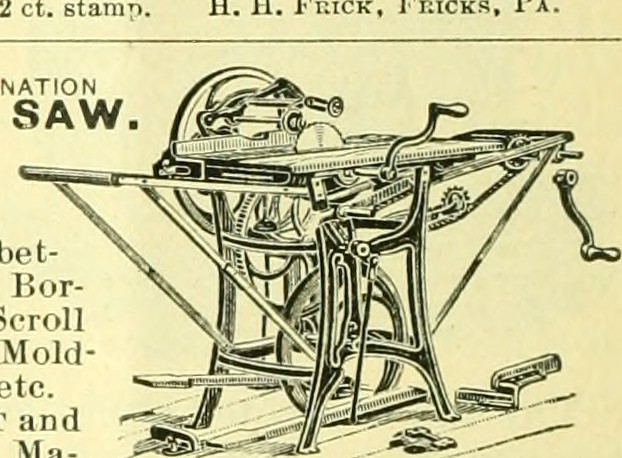
Using a fence to align the blade on a band saw is a simple process. To make sure the blade is parallel with the fence, place the fence on the sidewall of the band saw closest to the fence. Next, slide the fence across the miter slot until it is flush with its face. You may also be able to use a finger to feel along the miter slot to ensure the blade is aligned properly.
Before you can adjust the fence, it is important to place the blade guides. You must properly set up the band saw. The fence should be properly set up with a sharp knife. Adjusting the fence should be done if the blade moves. A jig, or bevel square, can be used to measure the drift angle. Here's a video showing you how to do that. You should first determine which fence is causing drift.
FAQ
How often do I need to buy new supplies
You will likely need to replace some tools over time. Hand tools will need to be sharpened regularly. Power tools will require replacement parts every so often. To avoid buying too much at once, try to spread your purchases out over a few months.
Where can I find free woodworking plans?
Woodworking plans can be found online without the need to purchase books or magazines. You only need to Google search. Enter "free woodworking", and you will see hundreds upon hundreds of websites offering free plans.
What is the difference between a hobbyist woodworker and a professional woodworker.
Hobbyists love making things from wood while professionals are more concerned with the quality of their work. Hobbyists usually take pride in their creations and often share them with friends and family. Professionals will spend hours researching designs before they begin working on a project. They will pay attention to every detail, from selecting the best materials to finishing the project perfectly.
Statistics
- The U.S. Bureau of Labor Statistics (BLS) estimates that the number of jobs for woodworkers will decline by 4% between 2019 and 2029. (indeed.com)
- In 2014, there were just over 237,000 jobs for all woodworkers, with other wood product manufacturing employing 23 percent; wood kitchen cabinets and countertop manufacturing employing 21 percent. (theartcareerproject.com)
- Most woodworkers agree that lumber moisture needs to be under 10% for building furniture. (woodandshop.com)
- If your lumber isn't as dry as you would like when you purchase it (over 22% in Glen Huey's opinion…probably over 10-15% in my opinion), then it's a good idea to let it acclimate to your workshop for a couple of weeks. (woodandshop.com)
External Links
How To
How to make wooden joints
This tutorial will show how to join 2 pieces of wood together. We will be using the "pocket-hole joint", which involves drilling holes in wood and then gluing them together. This method is great if your wood's straight and smooth. If your wood isn't straight or flat, you might want to try another method, such as dowel joinery. These are the steps
-
Drill Pocket Hole Joints. Measure and mark the location where you would like to place the pocket hole joint. Next, drill 3/4 inch holes in each end of each piece using a handheld drilling machine or jigsaw.
-
Sand Smooth. The wood's edges can be sanded to prevent splitting.
-
Glue Together. Apply glue on both sides of the wooden plank. Allow the wood to rest for five minutes before clamping it together.
-
Attach the Pieces together. After the glue has dried thoroughly, secure the pieces so that they are flush.
-
Trim Joinery. After the glue dries completely, trim off any excess wood around the joint.
Make sure to leave enough room between the pieces so that you can turn them inside and out.